GERENCIAMENTO DE ALARMES
ORGANIZE E
AUTOMATIZE SEUS
ALARMES
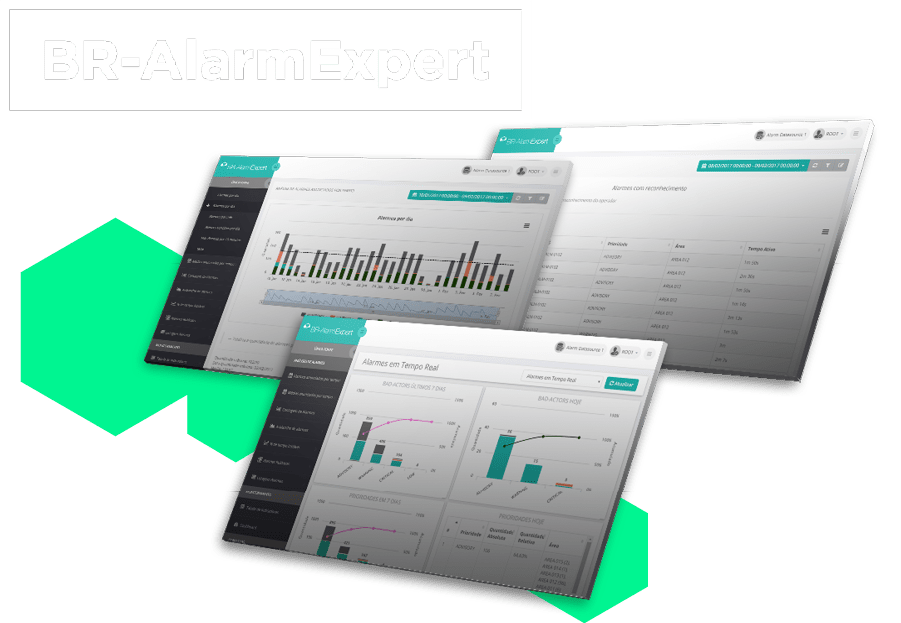
TENHA UM SOFTWARE COMPLETO
PARA ESTE PROCESSO
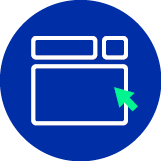
usabilidade simplificada
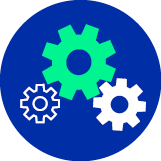
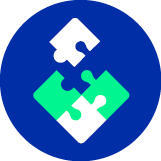
customizável
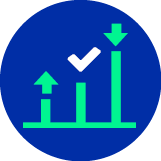
recomendados
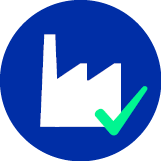
VEJA NA PRÁTICA:
O uso do software BR-AlarmExpert, combinado com reuniões periódicas com equipe multidisciplinar da planta, possibilitou a depuração do sistema de alarmes em uma mineradora.
COM O BR-ALARMEXPERT, VOCÊ:

Acessa via computador, tablet e smartphones

Integra usuários do sistema de domínio

Exporta dados para o Microsoft Excel ou seu editor de planilhas

Exporta gráficos em formato vetorial (SVG) e mapa bits (PNG)

Processa previamente os dados de forma e deixar o cálculo dos relatórios eficiente

Monta dashboards de acompanhamento de KPIs em tempo real

Segrega dados de alarmes de unidades industriais em fontes de dados distinta

Acessa estatísticas em diversas fontes de dados simultaneamente

Cria filtros nos relatórios por qualquer parâmetro de alarme
QUER SABER MAIS SOBRE O QUE O BR-ALARMEXPERT
PODE FAZER PELA SUA PLANTA?
GERENCIAMENTO DE ALARMES
Implemente boas práticas, usando softwares para monitorar o seu desempenho e metodologias para que seu sistema de alarmes seja útil, e não um problema.
VEJA OS RESULTADOS GERADOS
COM NOSSAS APLICAÇÕES.
Racionalização de mais de 4000 alarmes em empresa de energia
Com um sistema de alarmes sobrecarregado e com baixa conformidade, impactando a eficiência operacional, a empresa de energia buscava uma solução para aprimorar seu desempenho e ficar em conformidade com as normas técnicas EEMUA 191 e ISA 18.2. O projeto incluiu a...
Gerenciamento de Alarmes
Conheça os três principais problemas encontrados nas indústrias e como é possível solucioná-los com um projeto de gerenciamento de alarmes. O sistema de alarmes é uma camada crucial de proteção em plantas industriais, mas seu funcionamento inadequado pode comprometer...
Como reduzir o número de alarmes por operador em 97%
O uso do software BR-AlarmExpert, combinado com reuniões periódicas com equipe multidisciplinar da planta, possibilitou a depuração do sistema de alarmes em uma mineradora. Os operadores da mineradora tratavam com uma quantidade excessiva de alarmes ativados durante a...